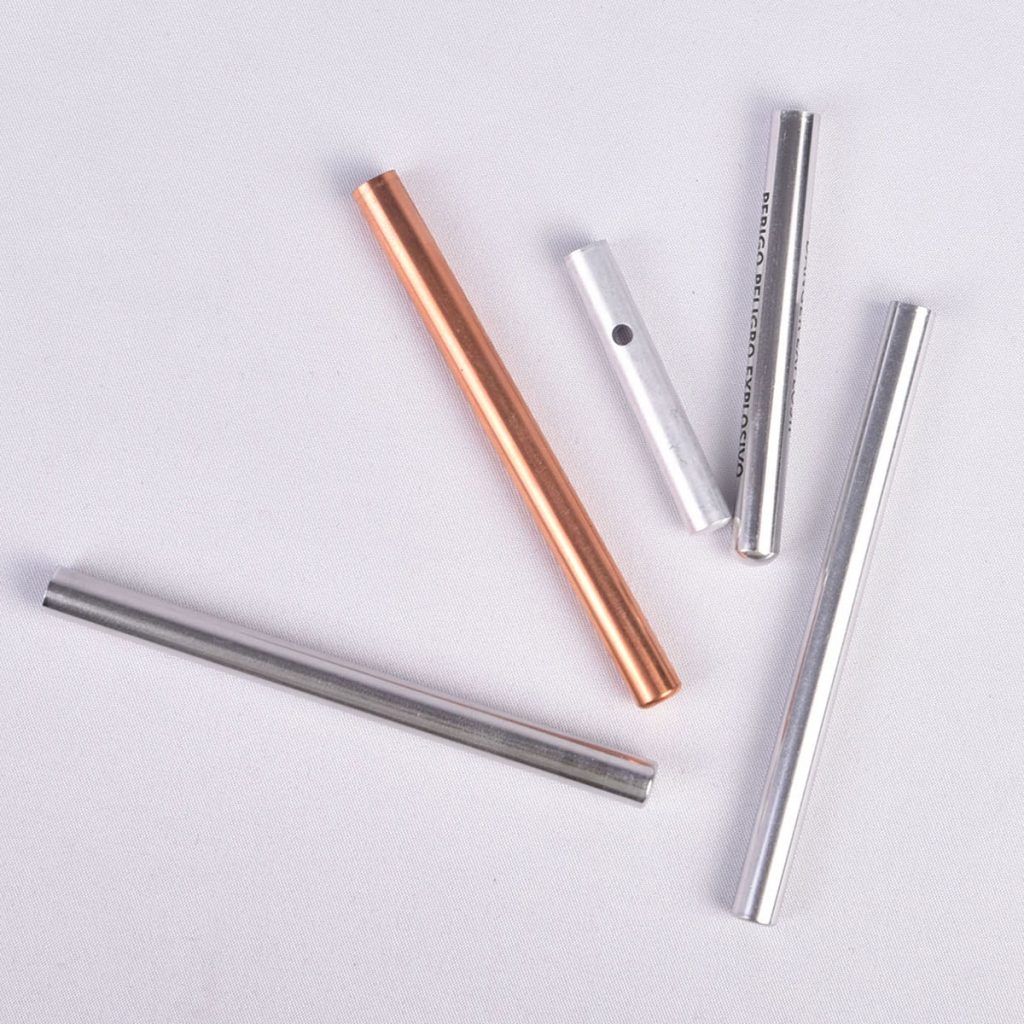
aluminum detonator blasting caps
- Product Name:Detonator Shells (Blasting Caps)
- Material: Aluminum AL5052, Copper, Brass, Stainless Steel
- Diameter(mm): 7.5mm, 7mm,7.2mm
- Height(mm): Height(mm): 46.5-95mm
- Tightest Tolerances:0.03mm
- MOQ: 200,000 PCS
- Custom size accept
- 1color Printing
Aluminum detonator blasting caps have a wide range of applications in various industries. Some of the most common applications include:
Mining: Aluminum detonator blasting caps are used in surface and underground mining operations to break up rock and extract minerals. The blasting caps are typically used in conjunction with other explosives, such as dynamite, to create controlled explosions that break up the rock.
Quarrying: Aluminum detonator blasting caps are used in quarrying operations to extract stone and other materials from the ground. The caps are typically used in conjunction with other explosives, such as ANFO (Ammonium Nitrate Fuel Oil), to create controlled explosions that break up the rock.
Demolition: Aluminum detonator blasting caps are used in demolition operations to bring down buildings and other structures. The caps are typically used in conjunction with other explosives, such as C-4, to create controlled explosions that bring down the structure.
Military operations: Aluminum detonator blasting caps are used in military operations for a variety of purposes, including clearing obstacles, destroying bunkers and other fortifications, and creating diversionary explosions.
Oil and gas exploration: Aluminum detonator blasting caps are used in oil and gas exploration to create controlled explosions that can help to locate oil and gas deposits.
Overall, aluminum detonator blasting caps are critical components in many industries where controlled explosions are required. They allow for precise and controlled explosions that maximize efficiency and safety.
Flour Test
- Flour Placed in The Cap and Removed
- If Any Residue Remains the Part is Rejected
- Acetone Test
- Acetone Applied to Area of Shell That Has Been Printed to Ensure Adhesion
Dimensional Inspection
- Standard Gauges
- Custom Gauges
- Optical Comparator
- Visual Inspection
Introduction
Aluminum detonator blasting caps are small explosive devices used to initiate larger explosions in mining, demolition, and other explosive-related industries. These caps are typically composed of an explosive charge enclosed in an aluminum shell with an ignition mechanism that is triggered by an electrical current. The purpose of the aluminum detonator blasting caps is to provide a precise and controlled method of initiating the larger explosion, ensuring maximum efficiency and safety during the blasting process. They are critical components in the mining and demolition industries, allowing for the safe and efficient removal of rock and other materials from construction sites or mining operations.
History of Aluminum Detonator Blasting Caps
The use of blasting caps can be traced back to the early 1800s when black powder was the primary explosive used in mining and demolition. The early blasting caps were made of paper or copper tubes filled with mercury fulminate, a highly sensitive explosive. The tubes were inserted into the explosive charge and ignited with a fuse.
In the early 1900s, aluminum became the preferred material for blasting cap construction. This was due to its light weight, high strength, and resistance to corrosion. The aluminum shell was filled with a more stable explosive, such as PETN or RDX, which allowed for greater control during the blasting process.
In the 1950s, advancements in electronics led to the development of electric blasting caps. These caps utilized a small battery-powered circuit to generate an electrical current that would ignite the explosive charge. This technology allowed for greater precision and control during the blasting process, as the electrical current could be timed and regulated more precisely than a fuse.
In the 1980s, electronic detonators were introduced, which allowed for even greater control over the blasting process. These detonators used microprocessors to precisely time and control the explosion, ensuring maximum efficiency and safety.
Today, aluminum detonator blasting caps continue to be a critical component in the mining and demolition industries. While advancements in technology have led to the development of more sophisticated detonation systems, aluminum detonator blasting caps remain a reliable and cost-effective option for initiating larger explosions.
Design and Construction
Aluminum detonator blasting caps are composed of three main components: the explosive charge, the aluminum shell, and the ignition mechanism.
The explosive charge is typically composed of a high explosive, such as PETN (Pentaerythritol tetranitrate) or RDX (Cyclotrimethylene trinitramine). The explosive charge is carefully measured and placed inside the aluminum shell.
The aluminum shell is a small, cylindrical container that encases the explosive charge. The shell is typically made of high-strength aluminum, which is lightweight, durable, and resistant to corrosion. The shell is designed to be as small and compact as possible, while still providing enough space for the explosive charge.
The ignition mechanism is a small electrical device that is used to trigger the explosive charge. The ignition mechanism typically consists of a small electric circuit that is powered by a battery. The circuit generates a small electrical current that is sent through a wire or bridge to the explosive charge. The electrical current ignites the explosive charge, causing a small explosion that sets off the larger explosion.
Advantages
Lightweight and durable: Aluminum detonator blasting caps are lightweight and durable, which makes them easy to transport and handle. They are less likely to be damaged during transportation and storage.
Easy to use: Aluminum detonator blasting caps are easy to use and can be quickly connected to the explosive charge. They can be timed and regulated more precisely than a fuse.
High resistance to corrosion: Aluminum detonator blasting caps are highly resistant to corrosion, which makes them ideal for use in harsh environments.
Can be used with different types of explosives: Aluminum detonator blasting caps can be used with a variety of different types of explosives, including PETN and RDX.
Conclusion
We are a leading manufacturer and supplier of aluminum detonator blasting caps in China. Our products are high-quality, reliable, & cost-effective. Contact us today for more information!